
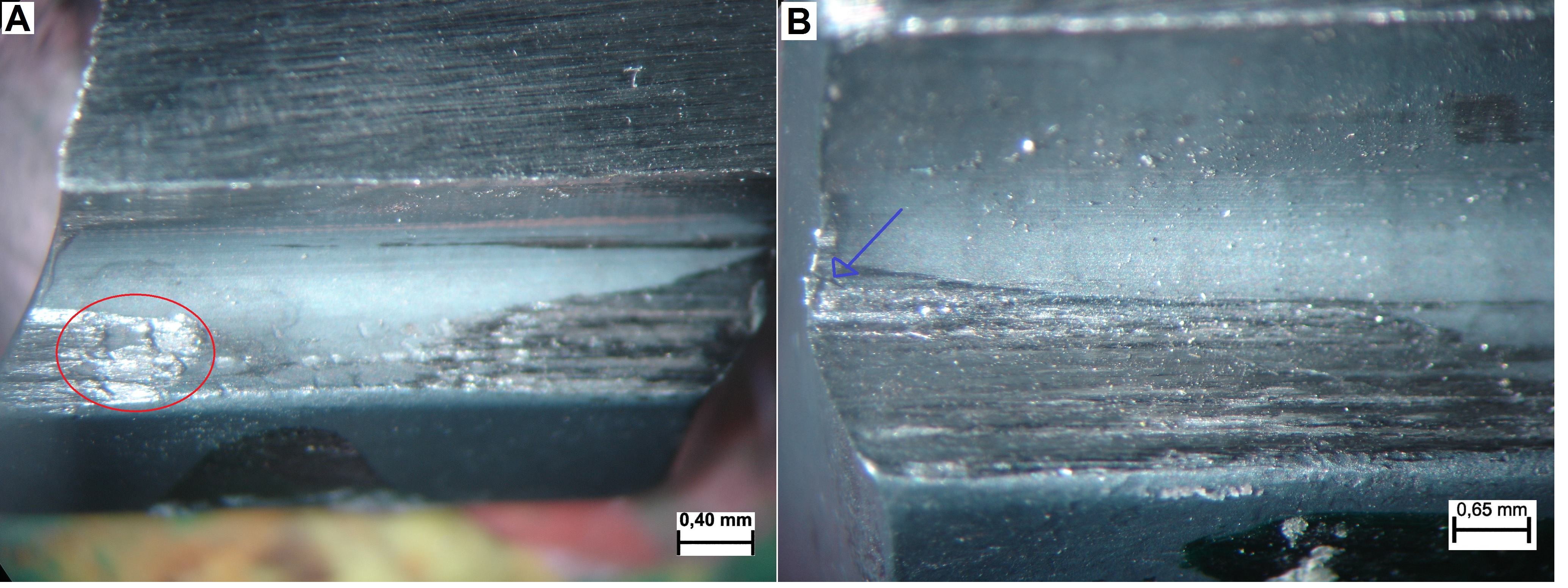
Figure 3 is a cross-sectional illustration of a prior art hollow metal object in the form of a fan blade Figure 2 is an elevational view of an exemplary hollow metal object in the form of a prior art fan blade for a gas turbine engine Figure 1 is an elevational cross-sectional view of an exemplary gas turbine engine The component is integrally formed and has regions comprising relatively different material compositions, the regions having gradual transitions of materials therebetween. In another aspect, a hollow metal component comprising a first side having interior and exterior surfaces, a reverse side having interior and exterior surfaces, the interior surfaces of the first side and the reverse side defining at least one cavity. In one aspect, a method of making a hollow metal component comprising the steps of: providing at least one core comprising a first side and a reverse side utilizing a first metal spray process to apply at least one metal or metal alloy to the first side of the core, resulting in a partially-formed structure comprising a first side and a reverse side and utilizing a second metal spray process to apply at least one metal or metal alloy to the reverse sides of the partially- formed structure and the core, resulting in a rough structure. There remains a need for improved manufacturing methods for making hollow metal objects which are cost effective and yield structures with good physical properties and dimensional control. Prolonged processing at elevated temperature can degrade material properties such as fatigue and ductility. Adhesive bonds may lack sufficient strength. Brazing and activated diffusion bonds may have local inferior property regions due to local alloying. Welding creates local heat affected zones which may require subsequent heat treatment. The bonding may be by fusion welding, solid state welding, diffusion bonding, activated diffusion bonding, brazing, bolting, or adhesive bonding. The component parts can be cut and formed from sheet metal, cast, milled and/or 'Super Plastic Formed'. Casting is affordable, but thin wall sections can be difficult to control and material properties can be poor. Hollow metal structures have been created by several methods. Hollow metal structures with good properties and dimensional control are often difficult to manufacture and may be expensive due to processing complexity and low yield with conventional processes. Hollow areas within the object may be utilized to reduce weight and/or impart other desirable structural properties. Many gas turbine engine assemblies include hollow metal objects, such as airfoils in the form of fan blades, and/or non-rotating stationary airfoils, such as guide vanes. The technology described herein relates generally to methods for making hollow metal objects, and more particularly to such objects for use as airfoils for gas turbine engines. HOLLOW METAL OBJECTS AND METHODS FOR MAKING The hollow metal component of claim 12, wherein said component has a lightweight material in said cavity. The component is integrally formed and has regions comprising relatively different material compositions, the regions having gradual transitions of materials therebetween.Ģ0. A hollow metal component comprising a first side having interior and exterior surfaces, a reverse side having interior and exterior surfaces, the interior surfaces of the first side and the reverse side defining at least one cavity. PRENTICE IAN FRANCIS OTT ERIC ALLEN WOODFIELD ANDREW PHILIP Ī method of making a hollow metal component comprising the steps of: providing at least one core comprising a first side and a reverse side utilizing a first metal spray process to apply at least one metal or metal alloy to the first side of the core, resulting in a partially-formed structure comprising a first side and a reverse side and utilizing a second metal spray process to apply at least one metal or metal alloy to the reverse sides of the partially- formed structure and the core, resulting in a rough structure. HOLLOW METAL OBJECTS AND METHODS FOR MAKING SAME
